The client, a medical supply distributor, needed a new facility to accommodate an increase in its volume without adding labor costs.
Increased fulfillment volume of medical distributor
The solution
PeakLogix integrated a custom solution in the new facility centered on technology. The fully automated design advances totes, and cases where appropriate, through the distribution center’s picking zones from start to finish.
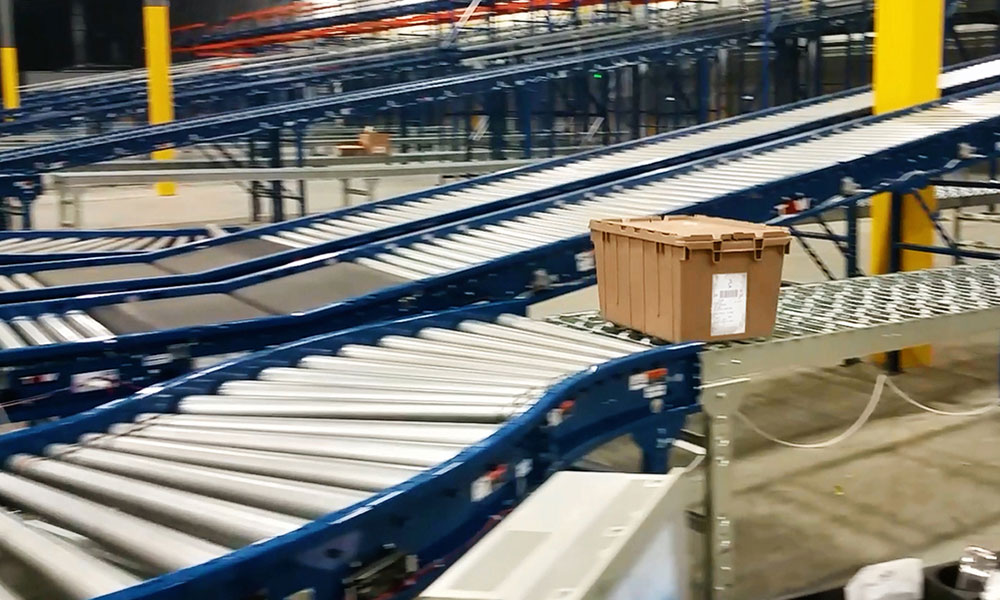
Controlled-Flow Gravity
Allows queuing of totes/cases on decline, essentially doubling the volume.
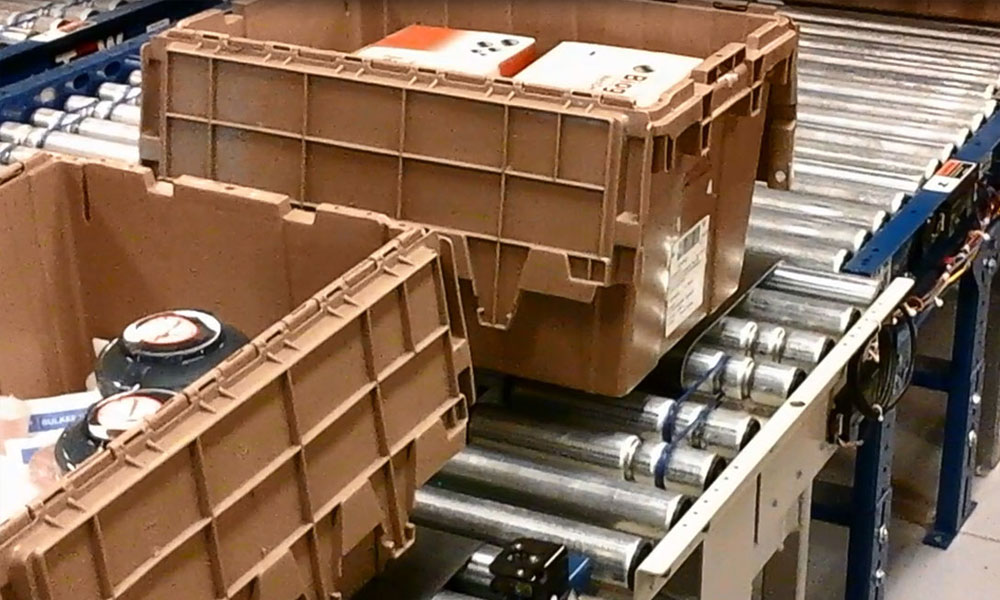
Case Turning Unit
Automatically turns the tote 90 degrees so the label is facing the picker.
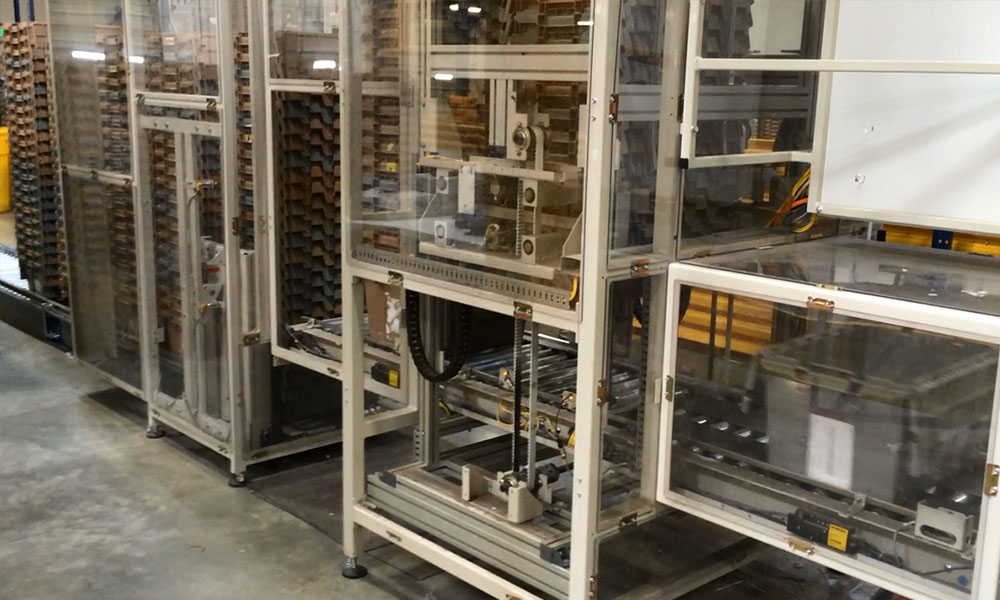
Tote Destacker
Queues stacks of empty totes and automatically singulates totes for induction into pick module.
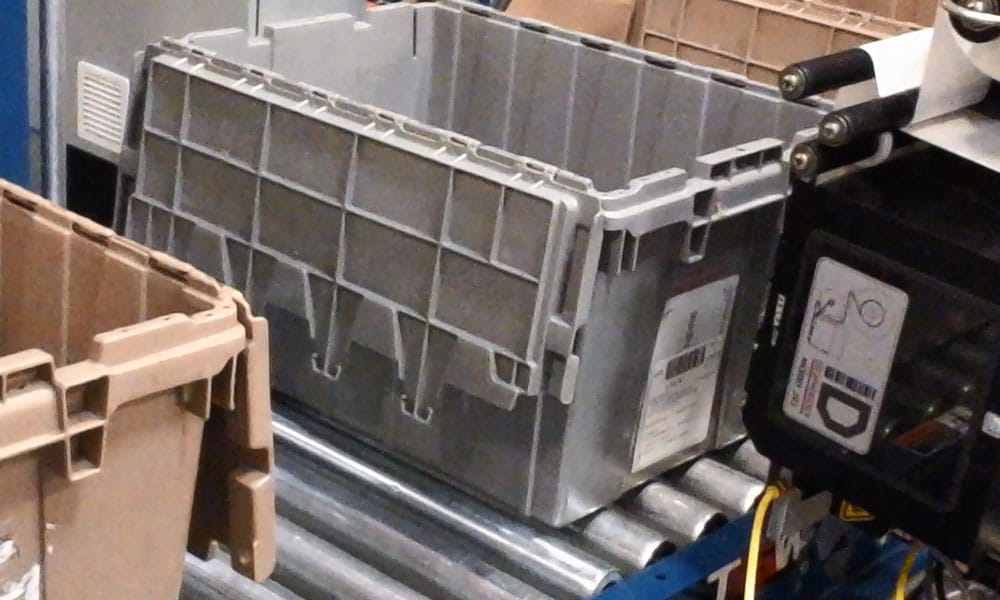
Print and Apply
Prints tote label and applies it to the tote, guaranteeing consistent label placement.
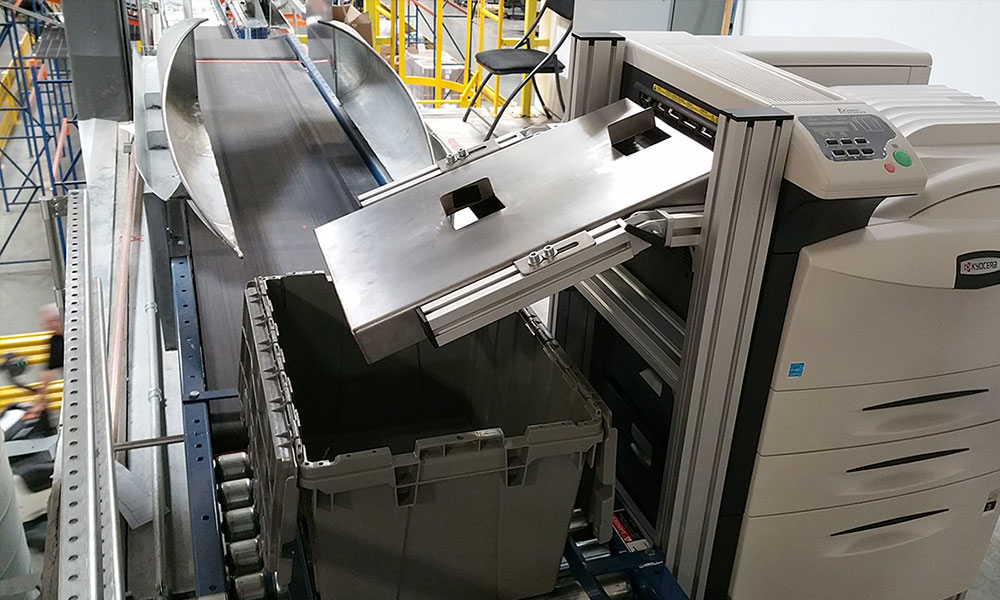
Print Drop
Automatically prints Pallet Content Sheet (PCS) and drops into tote.
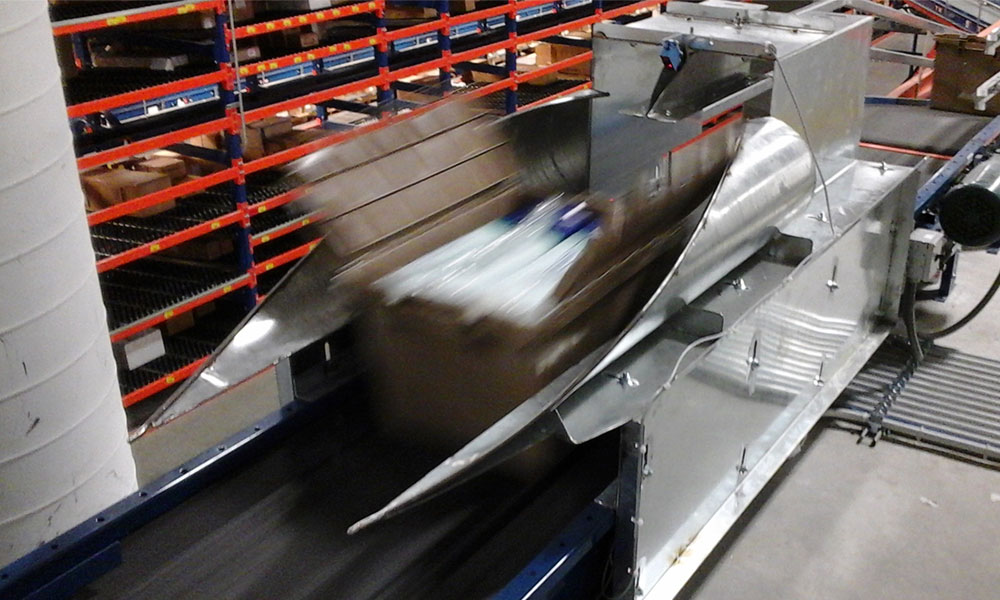
Automatic Tote Closer
Automatically closes totes after completion of picking and/or Print & Drop. Includes jam detection.
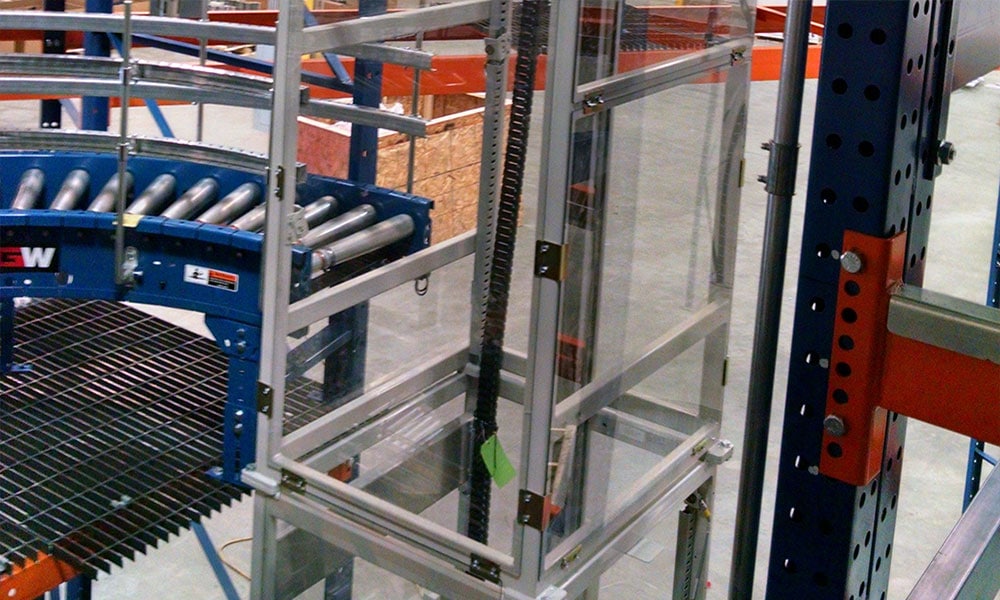
Vertical Reciprocating Conveyor
Moves totes between levels of pick module within a small footprint.
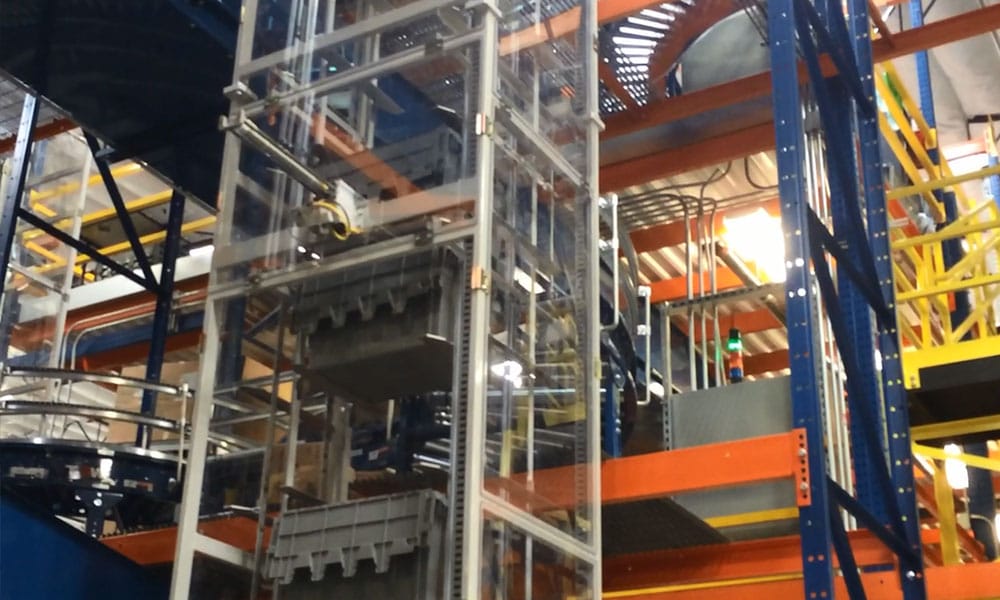
Vertical Indexing Conveyor
Helps to reduce tote traffic within the module, and reduces cycle time of pick process.
The results
Increased the amount of product fulfilled by 2x.
Various traditional elements were repurposed and paired with innovative technology to automate the process. The new design helped the facility reduce its cycle time, and increase fulfillment volume by 100%.