Crutchfield, an e-commerce electronics retailer, is successfully growing its business, which brings operational challenges to maintain or improve customer service. To meet demands and improve fulfillment efficiencies, Crutchfield considered increasing its labor force. Alternatively, the retailer explored implementing an automated process within its existing 40,000 sq. ft. distribution footprint without disruption to its daily sales requirements.
Increased efficiencies and operational expansions of e-commerce retailer
The solution
PeakLogix streamlined the facility’s picking process by designing and installing a picking system using automated, MDR conveyor and pick divert technology that integrates into the existing order processing software. PeakLogix removed the facility’s shipping bottleneck by refurbishing and repurposing the facility’s 12-year-old sorter. The print and apply machines were upgraded with Panther Industries current, all-electric models, reducing the facility’s three units to two and eliminating the need for compressed air. A new PC-based conveyor control system was installed to ensure accuracy and efficiency.
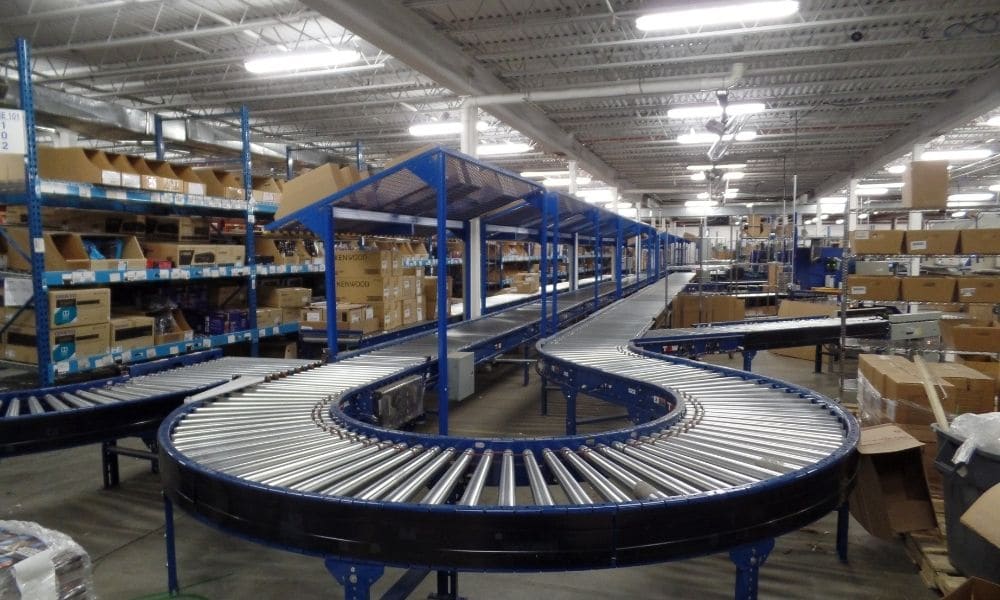
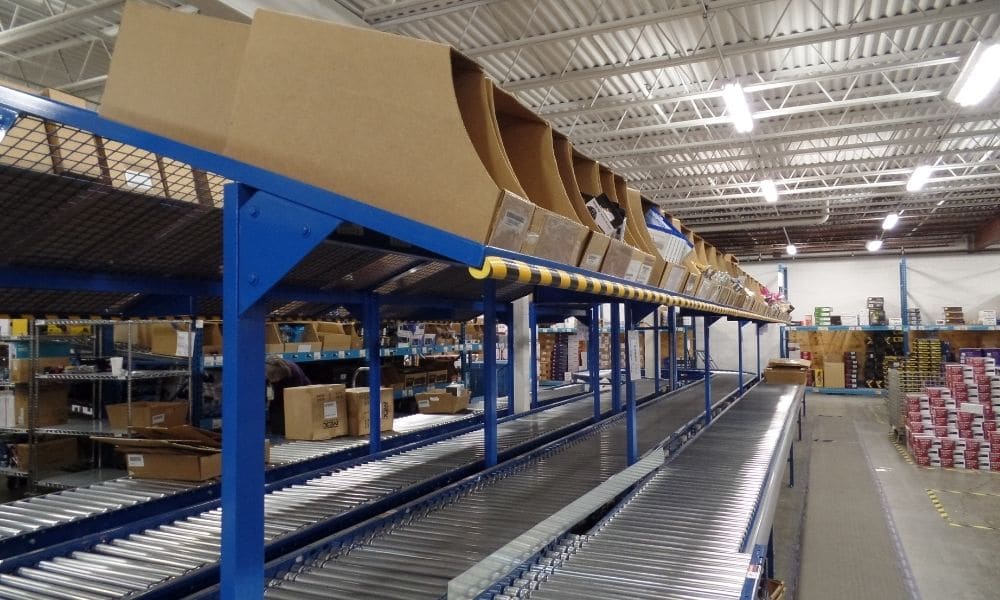
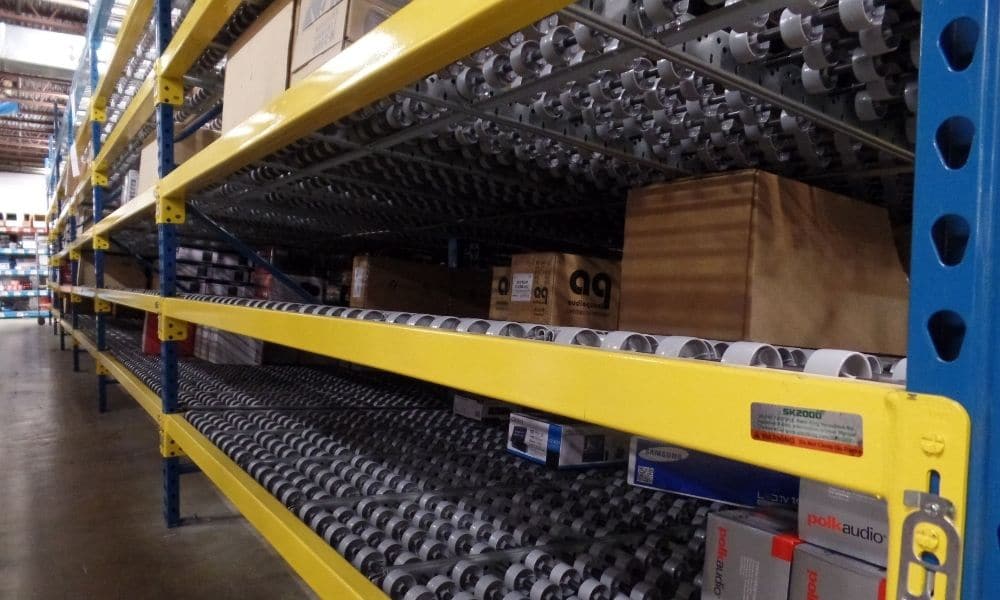
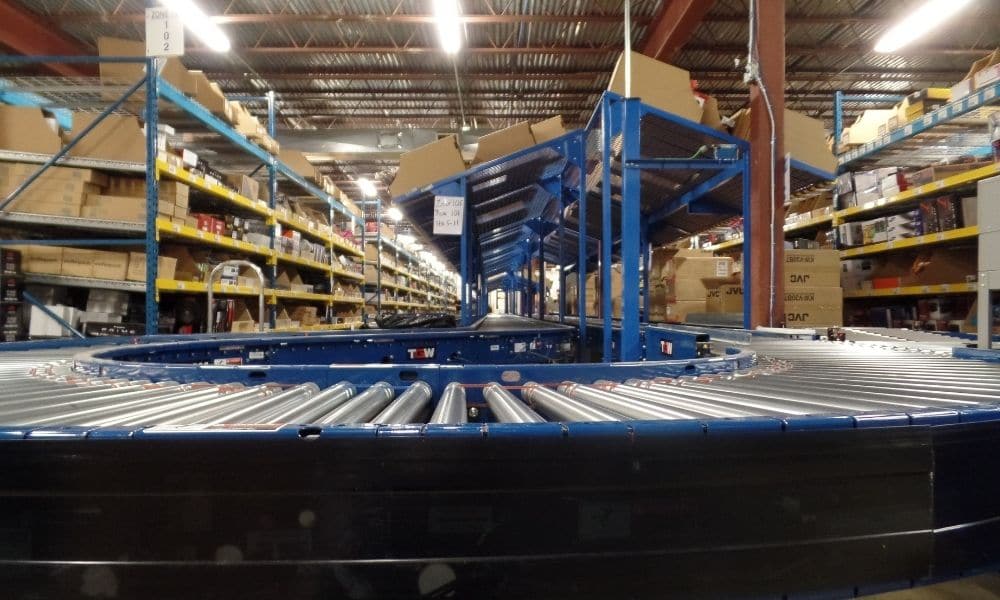
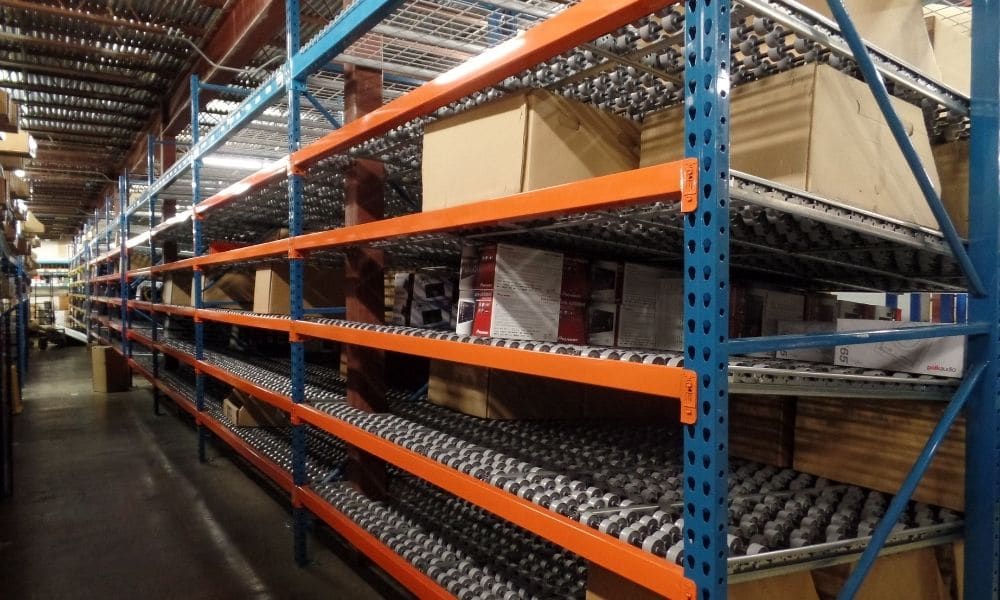
The results
25% gain in throughput and $250K in savings
PeakLogix streamlined Crutchfield’s facility to decrease labor costs and increase fulfillment, productivity and doubling shipping throughput. The new design achieved 25% gains in picking throughput and $250,000 annual savings.