The client desired automation for their picking process. Their previous manual system utilized a pick-to-cart methodology, using carts for transport from their pick aisle through shipping to the dock area. The client wanted to improve the flow of materials, increasing their daily line pick rate and distribution.
Increased throughput for clothing manufacturer
The client was able to increase their pick throughput to 18,000 lines per day over a 12 to 14 hour window.
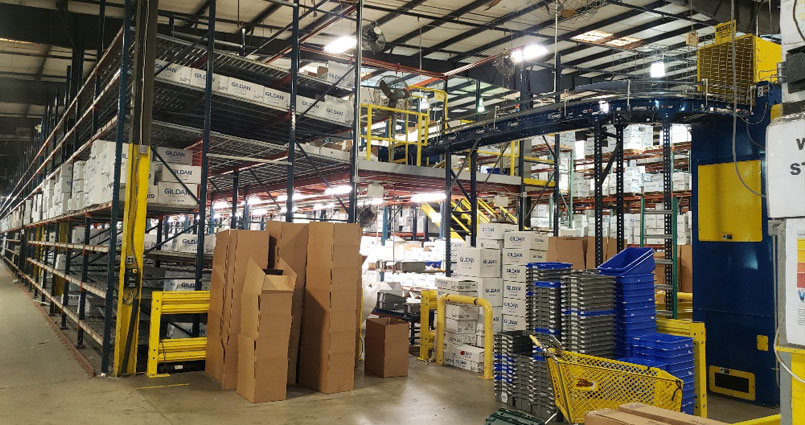
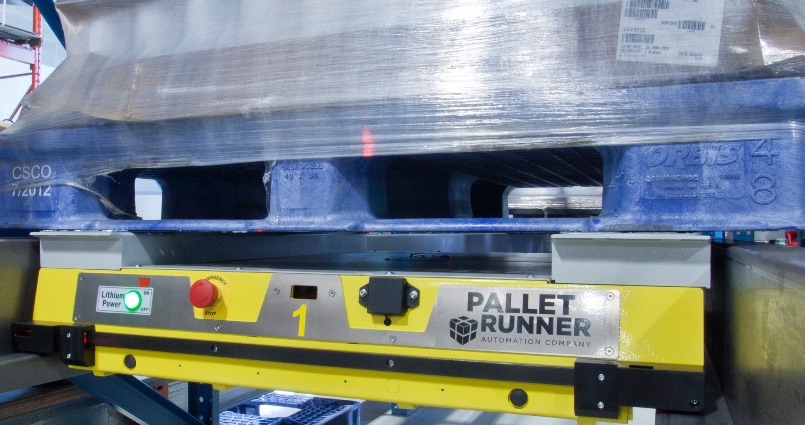
The solution
This module has 8 zones for picking across the 2 levels. Once cartons are picked complete and conveyed out of the module, each runs through a semi automatic taper, auto print and apply for 4” x 6” UPS shipping labels, and is sorted down the appropriate shipping lane.
The system provides 2,537 pick faces, as well as twelve 12’ deep push-back lanes, 3 return lanes for empty pallets, and above-conveyor shelving for increased SKU storage. The rate for the system, based on the client’s requirements, is 12 cartons per minute, however it is designed to run up to 16 cartons per minute.
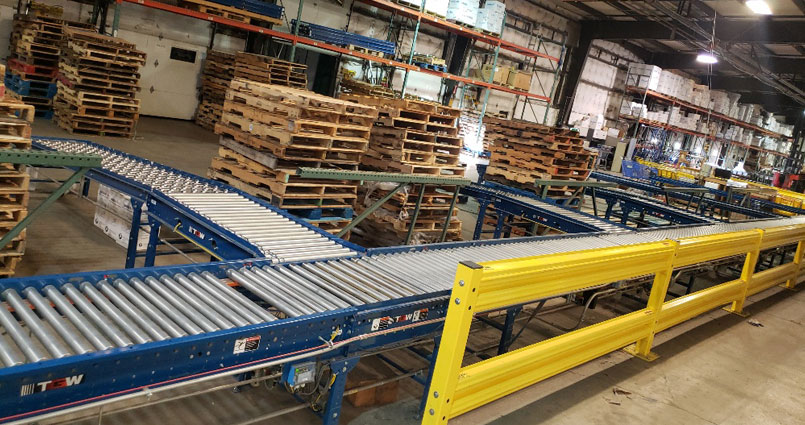
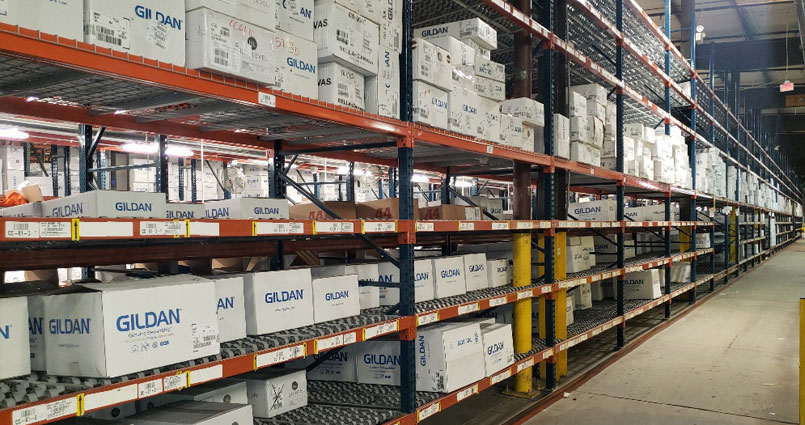
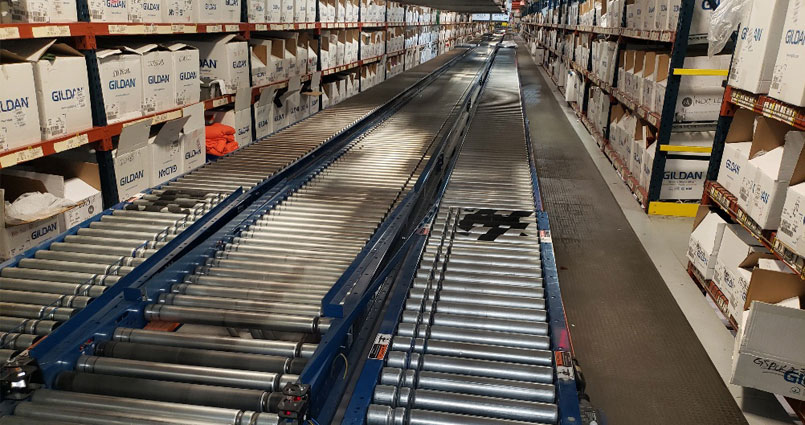
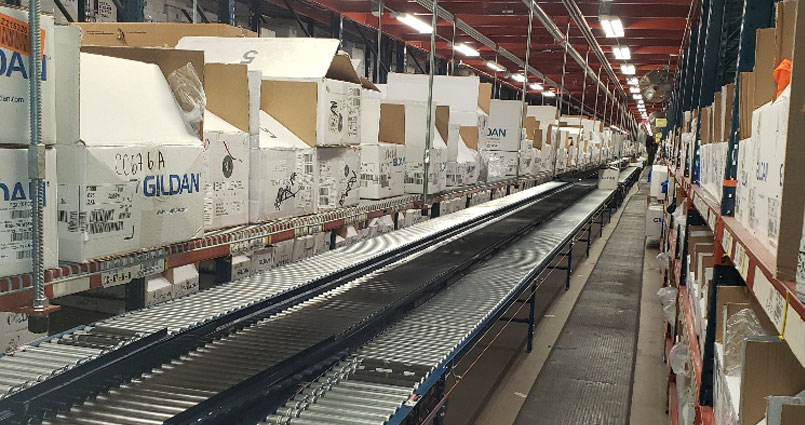
The results
Increased throughput drove 12% annual growth
The client was able to increase their pick throughput to 18,000 lines per day over a 12 to 14 hour window. This resulted in a 12% annual growth over a 4 year period to 28,000 lines per day. This 2-Level Pick Module system is staffed accordingly by the client and is not commonly seen in the industry.