Which Picking System is Right for Your Warehouse?
Warehouse efficiency is a competitive advantage, and the difference between Goods-to-Person (GTP) and Picker-to-Goods systems can mean the difference between slow, error-prone fulfillment and streamlined, high-speed operations. If your warehouse is still relying on manual picking, it may be time to evaluate whether a shift to automation could improve productivity, accuracy, and overall efficiency.
Understanding the Two Systems
Picker-to-Goods: The Traditional Model
Picker-to-Goods is the conventional method in warehouse operations. In this system, pickers travel to storage locations to retrieve items and bring them back for packing and shipping. While this method has been used for decades, it presents several operational challenges, including:
- High labor dependency – Workers spend a significant portion of their shift walking, which reduces productivity.
- Increased error rates – Manual picking can lead to mispicks, returns, and dissatisfied customers.
- Limited scalability – Expanding warehouse capacity requires additional labor, which can be costly and difficult to manage.
- Space inefficiencies – Picker-to-Goods systems require wider aisles for human movement, reducing potential storage density.
- Long training periods – New employees need time to learn SKU locations, further delaying efficiency gains.
Goods-to-Person: The Automation Advantage
Goods-to-Person (GTP) systems automate the picking process by bringing inventory directly to pickers at workstations. This is accomplished through technologies like Automated Storage and Retrieval Systems (AS/RS), robotic shuttles, vertical carousels, and conveyor systems. The benefits of this method include:
- Reduced picker travel time – Items are brought directly to workers, eliminating unnecessary walking.
- Higher picking accuracy – Automation reduces human errors and improves order fulfillment precision.
- Increased efficiency – GTP systems can achieve pick rates of 300-600 units per hour, compared to 50-100 in traditional systems.
- Better space utilization – Automated systems allow for high-density storage, maximizing available warehouse space.
- Scalability – Easily adapts to business growth and fluctuating demand, including peak seasons.
- Reduced training requirements – Employees interact with guided workstations rather than memorizing warehouse layouts.
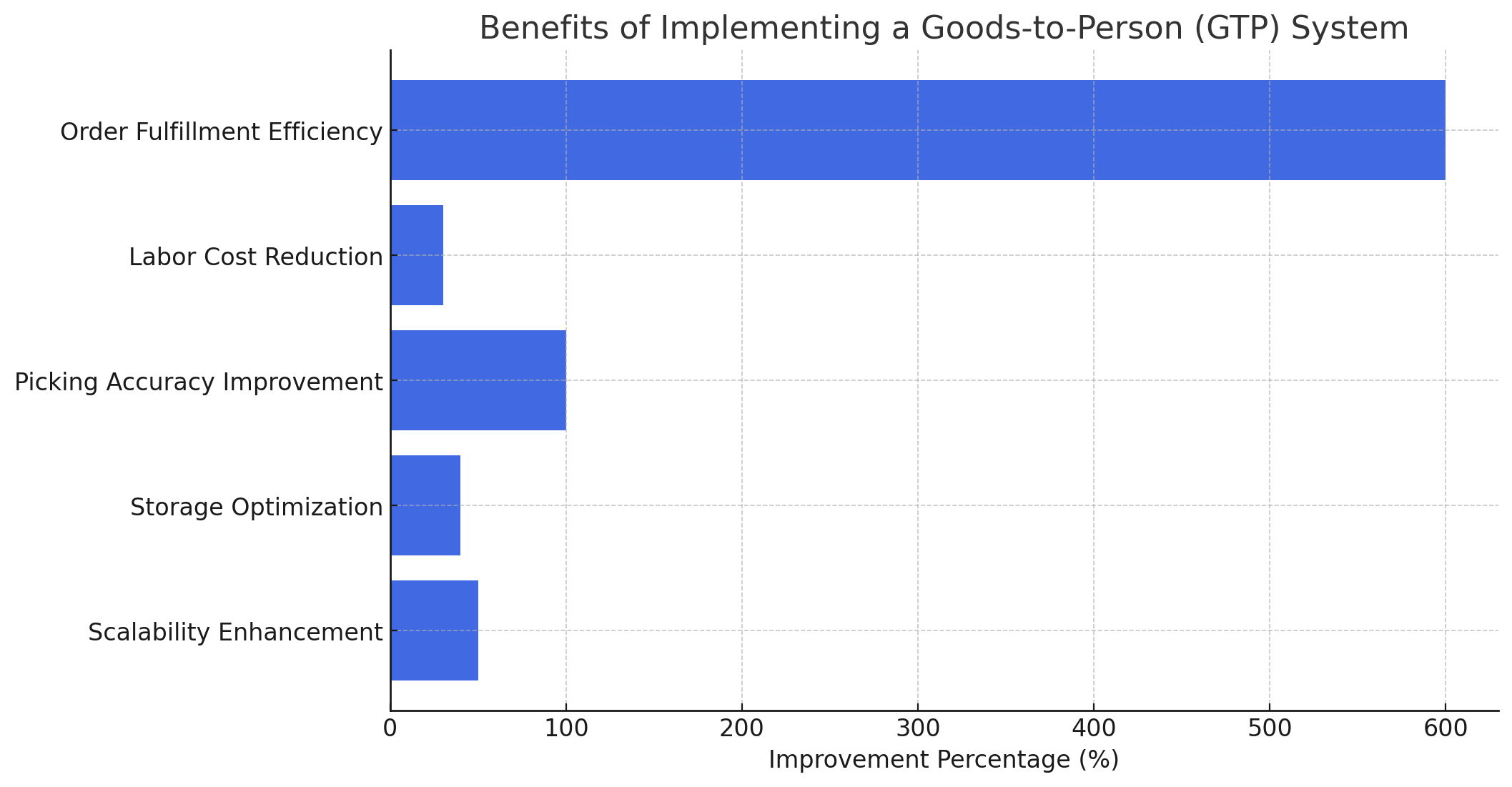
Real-World Example: How a Retailer Transformed Fulfillment with GTP
A national apparel and footwear retailer was struggling with fulfillment inefficiencies during peak seasons. Their Picker-to-Goods system required a large workforce to manage orders, leading to rising labor costs and delayed shipments. Despite hiring seasonal workers, bottlenecks persisted, affecting customer satisfaction.
By transitioning to a Goods-to-Person system with PeakLogix automation solutions, they achieved:
- 400% increase in picking speed
- 40% reduction in labor costs
- 99.9% order accuracy
- 30% more storage capacity due to high-density automated shelving
- Faster training times for new employees, reducing onboarding costs
PeakLogix GTP Solutions: A Smarter Way to Pick
PeakLogix specializes in tailored warehouse automation solutions designed to improve efficiency and scalability. Our GTP systems seamlessly integrate with WMS platforms, providing real-time tracking, intelligent slotting, and predictive analytics to optimize warehouse performance. Additional benefits include:
- AI-driven order prioritization – Ensures the most efficient picking process.
- Customizable workstations – Designed for ergonomic improvements and worker comfort.
- Regulatory compliance – Meets industry-specific requirements such as FDA and GMP for pharmaceuticals.
- Scalable solutions – Adapt automation as demand grows.
- Seamless integration with existing systems – Works with ERP and WMS software for full visibility.
When Should You Switch to GTP?
If your warehouse experiences any of the following challenges, it may be time to upgrade:
- Rising labor costs – If labor expenses continue to climb and recruiting workers is a challenge, automation reduces dependency on human pickers.
- Frequent picking errors – If returns due to mispicks are increasing, GTP ensures precision in order fulfillment.
- Seasonal demand fluctuations – If your warehouse struggles to keep up with peak season orders, automation provides scalable solutions.
- Limited storage capacity – If space constraints are limiting growth, GTP allows for high-density storage.
- Long training times – If new hires take weeks to get up to speed, GTP systems simplify the process.
Is It Time to Upgrade?
If your warehouse struggles with slow fulfillment, high labor costs, or frequent errors, transitioning to Goods-to-Person automation could be the solution you need.